Environmental safety is defined by the guidance, policies, and practices enforced in order to ensure that the surrounding environment is free from hazards that will warrant the safety and well-being of workers and employees, residents near industrial operations, as well as the prevention of accidental environmental damage. The surrounding areas include industrial facilities, work areas, and laboratories. Environmental safety is a crucial issue for any industrial activity as negligence and non-compliance heighten the risk resulting in injuries, illnesses, and accidental environmental releases.
With the aim to ensure safe and healthy working conditions for working employees, the United States Congress has passed the Occupational Health and Safety Act (OSHA) of 1970, to enforce health and safety standards and to educate and train employers and employees to observe and comply with the developed policies and guidance.
The following outlines OSHA’s role in preventing unwanted injuries and diseases that will render a person’s impairment of health or functional capacity from occupational exposure to hazards, as well as its part in identifying unsafe practices, and addressing workplace safety issues.
- OSHA is responsible for ensuring that workplace safety and health programs are implemented, and employers abide by its regulations.
- OSHA sets safety and health programs whereby facilities and establishments must prepare its Environment Health and Safety (EHS) program, provide necessary training to its employees and staff, conduct inspections, tests, monitoring, and audits, and create a filing and record-keeping system for these activities.
- OSHA is responsible for establishing and enforcing federal and state inspectors.
- OSHA organizes public education and consultation forums and seminars as well as the provision of safety information materials availability
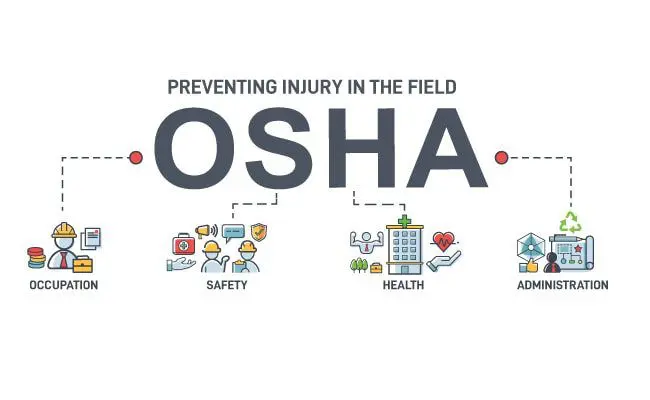
Environmental safety is usually divided into three subcategories: Occupational safety and Health Programs, Environmental Control, and Chemical Safety.
Personal injuries and illnesses resulting from work-related operations and situations impose a hindrance to a person’s ability to become productive. An injured or disabled employee carries the burden of medical expenses and wage loss. It also translates to the company and the state’s economic loss. For this reason, the Occupational Safety and Health (OSH) Program is strictly implemented for businesses that handle hazardous chemicals, fumes, and emissions and wastes.
Environmental control is another aspect of environmental safety that deals with the management and proper disposal of pollutants and other sources of threat to the environment. Environmental controls include engineering and administrative control solutions to minimize hazard exposure through inhalation, skin and eye contact, ingestion, and injection.
The following are some examples of general environmental controls for facilities:
- Safety color codes for pipes and cans
- Marking hazards
- Provision of safety signs (Danger,
- Caution, and Instruction signs)
Lockout/Tag-out (LO/TO) - Provision of sanitation facilities
In managing workplace hazards, the following are processes for controlling exposure that poses health and safety risks. The hierarchy of control is ranked from the highest reliability and efficiency to the lowest.
Elimination of the hazard – total elimination of the hazard is the most preferred and effective solution to control risks and hazards.
Substitution – reduce manual exertion on tools with power tools, reduce heavy items with light ones, substitute a harmful chemical with another chemical that is less or not hazardous e.g., no lead paint, natural pesticides, water detergent solutions
Engineering controls -design of systems or modification of an existing layout or process that will reduce exposure to hazards
- Process controls-electric motors over diesel engines, wet method drilling over dry method, automation and remote control
- Isolation or enclosure-physical barriers that keep the risk and the worker away from coming into contact with each other
- Ventilation-removes or dilutes air contaminants to avoid its dispersion at workstations
Administrative controls – work practices and standard operating procedures that can alter how and when the work is done.
- Access restriction,
- Scheduled machinery maintenance,
- Job rotation to limit exposure
- Personal hygiene
Personal Protective Equipment (PPE) – PPE is the last line of defense but must not be the only method to reduce exposure. PPE includes eye protection, face shields, footwear, and gloves.
Chemical safety is another environmental safety concern that primarily focuses on ensuring that hazardous chemicals are properly stored, used, and disposed of. Businesses must be aware of the chemical safety regulations, as it not only saves lives and preserves the environment, but also prevents regulatory penalties and fines for non-compliance.
Chemical Hazards and Toxic Substances
- Toxins
- Acute-short term toxins
- Chronic-long term toxins
- Irritants-chemicals that cause irritation of the skin and eyes
- Sensitizers-changes proteins
- Tumorogen-causes tumor growth
- Mutagen-substances capable of altering genes with generational impact
- Teratogen-alter fetuses, non-generational impact
- Reactive chemicals-chemicals that react violently upon contact
- Corrosives
- Acids
- Bases
- Combustible or
- Flammable materials
- Combustible-solid, liquid, and gas
- Flammable=solid, liquid, and gas
- Pyrophoric-gases capable of instantaneous ignition
In order to implement a feasible environmental safety program, the following are recommended core elements:
Top Management Support
The direction to commit to EHS programs and to continually improve its mechanism must start from top management. The program’s responsibilities, objectives, and expectations must be defined by top management, who should also allocate the appropriate resources for the implementation of the program and communicate the plan to employees. Management leadership encompasses owners, managers, and supervisors who create a culture that is safety centered and who are the first to reinforce these elements.
Hazard Identification and Assessment
A facility must establish the procedures required to identify workplace hazards and evaluate existing risks for routine, non-routine, and feasible emergency situations. Once hazards and risks are identified, employee exposure level and existing control measures must be assessed. A plan of how periodic inspections are implemented and how new threats are identified must also be strategized.
Employee participation
Employee participation in the EHS program is an essential part of its successful implementation, from EHS planning, creating goals and objectives, reporting risks and hazards, monitoring, up to the incident investigation.
Employer and worker’s safety training and education
Employer’s managers must be trained and informed on safety concepts, their role in the implementation of it, and their responsibility of protecting the worker’s welfare at all times. All workers must be trained on how the safety program works, their participation in it, and the skill to identify and recognize risks and hazards.
Hazard prevention and control
This process entails the identification and selection of the methods that will be used in preventing, eliminating, and controlling workplace hazards. Controls must follow a hierarchy of engineering solutions first, then safe practices, administrative controls, and personal protective equipment.
Evaluation and Improvement
The implemented control measures must be evaluated periodically to check for their efficiency. The process by which the program is monitored must be established along with the metrics used to verify the implementation of the program and identification of opportunities for improvement.
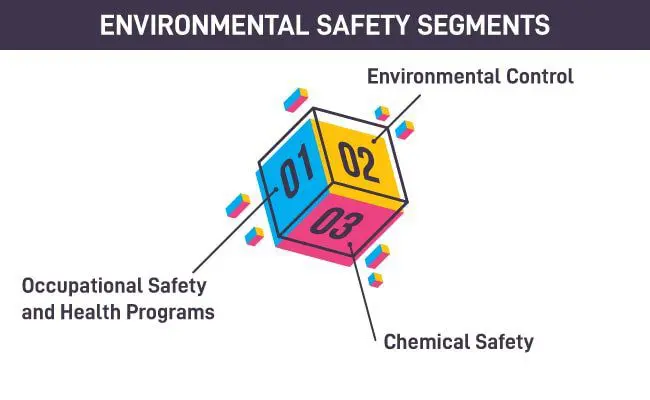
Hazardous Waste Operations and Emergency Response (HAZWOPER) are guidelines provided and updated by the Occupational Safety and Health Administration (OSHA) that focuses on the regulation of dangerous and hazardous substances and wastes and the provision of emergency responses within the United States. It is developed for workers that have direct exposure to the hazard and are in charge of the storage, clean-up, treatment, and disposal of hazardous materials. The HAZWOPER standard is aimed to protect the workers and to ensure safety and efficacy in handling dangerous materials by providing information and training for employees as required by OSHA.
HAZWOPER is applied to the following employers involved in the performance of the following:
- Cleanup operations on hazardous waste site as required by a government body (federal, state, or local)
- Corrective actions for Resource
- Conservation and Recovery Act of 1976 (RCRA) recovered sites
- Voluntary cleanup initiatives by a government body (federal, state, or local)
- Operations related to the treatment, storage, and disposal of hazardous substances and wastes
- Emergency response to the accidental release of hazardous substances that poses a significant immediate threat to the worker’s health and safety.